How much energy is required during in situ thermal remediation (ISTR) project to reach site goals? It’s a question we often hear, because not only does energy usage impact project cost, it is also one of the major resources that contributes to the environmental footprint (even though sustainable energy sources can be used).
Thermal conductive heating (TCH), electrical resistance heating (ERH), and steam enhanced extraction (SEE) are widely used thermal technologies capable of effectively remediating a variety of chemicals from different geological settings, ranging from tight clays to permeable sands. But understandably, the energy required to implement these technologies may determine if it’s the best choice for your specific site. To help you make that call, we took a dive into our database of completed thermal projects to see what our real world experience has been regarding energy use.
What Determines Energy Usage on a Thermal Remediation Site?
It is crucial that sufficient energy is delivered to the subsurface to overcome site heat demands, balance heat losses, and to facilitate enough boiling and steam stripping of the site contaminants to meet remedial objectives. There are two key site-specific parameters that dictate the power usage at your thermal site: the geology and the contaminants.
Geology: Soil parameters affect the soil heat capacity, and therefore the energy required for increasing the temperature from ambient to the boiling point. The mineralogy, along with the air-filled and water-filled porosity, are the major drivers for the soil heat capacity. The specific heat capacity of water is about five times higher than the heat capacity of the soil particles, therefore, initial water content governs the energy usage. Excluding heat losses, the typical energy usage to get from ambient temperature to 100°C is on the order of 40 to 60 kWh/cy but varies with porosity and saturation as indicated in the figure below.
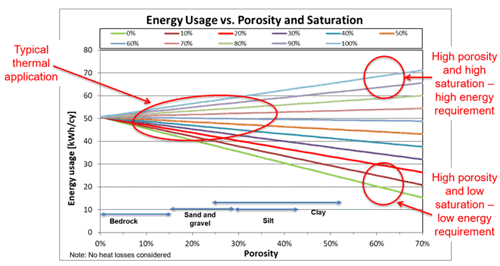
Contaminants: Site contaminant characteristics also affect energy usage. Key chemical parameters like solubility, Henry’s Law Constant, and vapor pressure all govern the volatility and therefore the energy required for proper mobilization during the thermal remedy.
The amount of steam generated in situ (i.e., steam stripping) needed for removal of the contaminants is often a good measure of how easily a chemical will be removed. This volume of steam is presented as a percentage of initial pore volume and represents a critical thermal design parameter. Volatile VOCs like PCE and TCE typically require less steam stripping (boil-off of typically 20-30% of the pore volume) compared to, for instance, xylenes and chlorobenzenes (boil-off of typically 25-35% of the pore volume). Naphthalene is considered both a VOC and SVOC and can still be removed at the boiling point of water; however, this requires more steam stripping and a longer duration held at the boiling point (e.g., boil-off above 35% of the pore volume), which increases energy usage.
A high temperature application is required for chemicals like most pesticides, dioxins, heavier hydrocarbons from manufactured gas plants and creosote sites, polycyclic aromatic hydrocarbons (PAHs), polychlorinated biphenyls (PCBs), and per- and polyfluoroalkyl substances (PFAS). High temperature treatment requires all the pore water to be evaporated (boil-off of 100%) because the temperature in the soil will buffer at the boiling point of water until all water has been removed.
Water requires a lot of energy to evaporate. In fact, about 0.3 kWh of energy is required to boil off and remove one pound of water from the subsurface. Therefore, a saturated cubic yard of soil with a porosity of 30% and 40% will require about 144 and 191 kWh of energy, respectively, to dry out—again, no heat losses are considered. As a result, the total energy usage is closely related to the contaminants targeted.
How Much Energy is Used on a Thermal Remediation Site?
So going back to the database review… By looking at previously completed TCH, SEE, and ERH projects targeting 100°C, we found the following average energy consumption for VOC and SVOC treatment.
Our datasets indicate a big differential in power usage—even within the same technology for the same contaminants. Both the contaminants and site-specific conditions affect energy usage.
We also found that typical lighter-end SVOCs require approximately 30% more energy to meet performance goals, compared to VOCs.
The theoretical energy (excluding heat losses) to increase the soil temperature from ambient to the boiling point of water and boil off between 20 to 30% of the pore water is approximately 70-115 kWh/cy. In reality, between 228 and 251 kWh/cy was used for VOC removal across the three heating technologies. The difference is due to varying site conditions and heat losses. Site-specific heat losses, which are determined by the size and shape of the site as well as local groundwater flow, need to be properly evaluated for all sites.
Now that you understand how energy use is estimated for thermal remediation projects and how that compares to real life data, you can better understand and evaluate if these heating technologies and their associated costs are right for your projects.
If you’d like to learn more about energy usage or other aspects of thermal technology, click on “Watch Now” for a webinar hosted by Cascade, Ask the Experts: Thermal Remedies. Where a panel of TerraTherm experts (including myself) answer all your questions.
10.27.22
Steffen Griepke
Steffen Griepke is the Vice President of Technology at TerraTherm. In this role, he helps clients determine if a thermal remedy would work on their project site and, if so, which thermal technology or combination of technologies would be the most cost-effectiv...