If you have a site that is impacted by subsurface contamination and targeted for thermal remediation, it will require in-depth research and calculations to determine how best to design the thermal remedy and to predict remediation progress (e.g., schedule, power usage, etc.). Before going down the thermal route, you will need to understand and have your source zone properly delineated and have key site parameters such as geology, hydrogeology, and contaminant defined, in order to move forward with site remediation process and design. Sites without a proper and detailed site characterization will lead to inaccurately estimated project parameters such as cost, duration, and equipment types and sizing.
Successful thermal remediation has occurred at sites made up of bedrock, and others made up of clays or even a mix of many different geologies. Some sites are very large in area and volume, while others can be fairly small and shallow. Successful sites can have deep groundwater tables, and some can be completely saturated. Each site is different and thus needs a flexible modeling and predictive tool that can be customized for actual site conditions in order to provide accurate design information and performance predictions and ensure a successful in situ thermal remediation (ISTR) project.
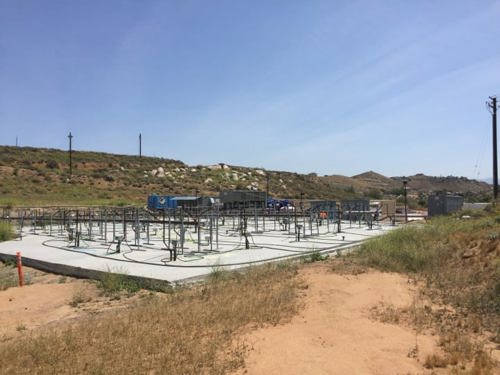
How does a numerical model work?
In addition to typical engineering calculations, the use of numerical models can also be very useful in designing a successful thermal remediation project. Numerical modeling is used to figure out how the site and the contaminants of concern (COCs) will react to the energy or heat input to the subsurface and the vapor and liquid extraction systems. This will determine the operational duration, the best treatment system for the site, the energy usage, and many other parameters. These parameters also help to determine the cost of thermal remediation.
One very efficient and successful numerical modeling approach is to use a multi-layered, transient box model to track the changes in the energy state of the system by calculating the water and energy balances of the system at each time step.
Figure 2 provides a conceptualization of how the energy and water balances are calculated in the model.
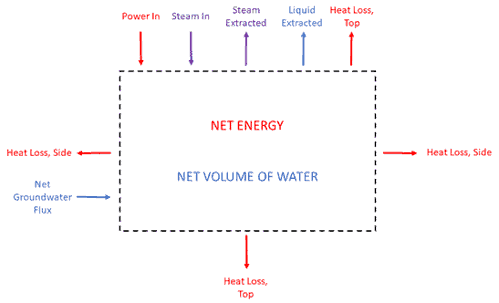
The transient box model can incorporate multiple layers that correspond to the geology seen at the site, with each layering having its own geologic and hydrogeologic parameters.
For example, each layer can have a custom porosity, hydraulic conductivity, groundwater gradient, etc. This information is typically provided by the consultant/client in the form of geologic descriptions, geologic cross-sections, soil boring logs, geophysical and hydrogeologic soil analyses, electrical resistivity measurements, water table maps, aquifer tests (slug/pump tests), contaminants of concern and clean-up goals, and contaminant distribution maps.
The importance of accurate and detailed site parameters
The site’s parameters need to be accurately represented in the numerical model to be able to accurately calculate energy input, energy transfer, and heat-up within the subsurface of the site. We base our model on detailed site information provided by the client such as geology, hydrogeology, key soil parameters, and a 3D understanding of the treatment volume. To run the numerical model of the site requires assimilating all the data received from the client and determining the optimal layer distribution that accounts for changes in lithology, hydrological boundaries, and the geometry of the target treatment zone (TTZ). Each layer is treated as its own element or box through which energy and water are transferred, allowing individual portions of the treatment volume to be examined more carefully. Figure 3 shows an example of distributed layers in a site’s numerical model.
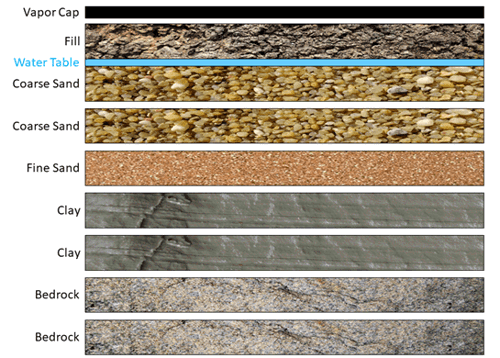
Once all the custom parameters for a site are entered into the model, the model outputs information for each layer. This information includes an energy and water balance, subsurface temperature curves, operation duration, vapor and liquid extraction rates, and estimated project utility usage (e.g., electricity for TCH or ERH or natural gas for steam) Figure 4 shows an example of model predicted subsurface temperature curves for a site.
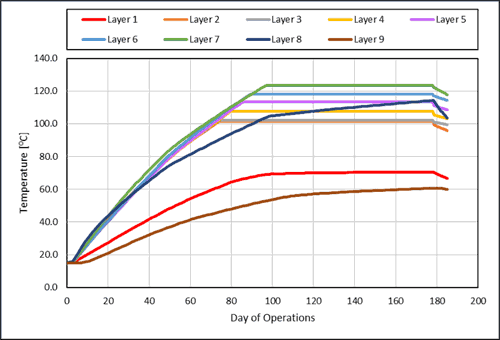
Figure 5 below shows an example of how the model predicted heat-up can be used to track actual site heat-up progress. This type of evaluation can be used to adjust energy input and vapor and liquid extraction strategies to ensure that the project is completed on schedule.
The figure also shows that through a simplified representation of the treatment volumes and when the subsurface is properly understood, modeling can be an accurate and reliable tool for predicting progress towards target temperature. In summary, the primary use of a model is to understand the total volume of soil, water, and air in the model domain and how much groundwater is flowing through to estimate the site heat capacity and therefore the energy required to heat the volume to the target temperature.
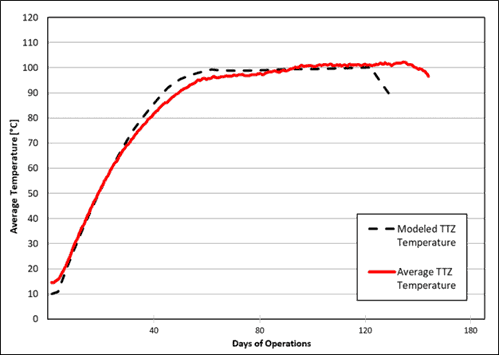
A model is also useful in the design phase for evaluating potential challenges, such as groundwater flow at certain depths, the importance of the R-value of a vapor cover, and sensitivity to starting groundwater levels and saturation. By simulating high and low values of key factors, sensitivity studies are developed that indicate where to focus and optimize the design. Figure 6 is an example where the upward flow of groundwater and a poor vapor cover led to less-than-optimal heating of the site.
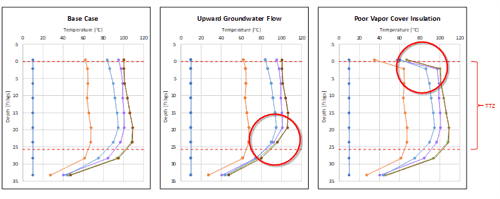
Overall, a model of the thermal remediation processes provides a solid baseline for clients and engineers to know what to expect during a project and when operations are not going according to plan. It is useful for verifying and informing the design, tracking the progress of a project during operations, and reflecting on how a project performed relative to expectations throughout its operation.
Check out this webinar recording about thermal modeling if you are interested in learning more: https://terratherm.com/webinar/in-situ-thermal-remediation-modeling-the-basis-of-design/
01.13.22
Sophia LaRoche
Sophia LaRoche is one of our Data Managers. As a Data Manager, she monitors and processes real-time data that comes in from the field and shares with the project team. She is also involved in system design support, work plan preparation, and engineering fi...