No matter the thermal heating technology, one of the biggest balancing acts when it comes to in situ thermal remediation (ISTR) is injecting enough energy into the subsurface to sufficiently heat the target treatment zone (TTZ), while also extracting enough fluids to maintain hydraulic and pneumatic control of the TTZ. In today’s blog post, I will explain what it means to keep both hydraulic and pneumatic control and how these metrics are monitored.
What does it mean to maintain hydraulic and pneumatic control during ISTR?
During a thermal remedy, the main mechanism for the removal of volatile organic compounds (VOC) from the subsurface is through volatilization and vapor extraction. Because of this, it is key to ensure that both the hydraulic and pneumatic gradients at a site are directed towards the treatment area such that contaminants mobilized by the thermal system are not spread outside of the TTZ. That means pneumatic control of a TTZ is achieved when the flow of vapor is nearly evenly distributed across all vapor extraction points throughout the ISTR wellfield and an inward pneumatic gradient is established.
Likewise, at sites where groundwater is flowing, increased solubility with temperature may mobilize contaminants in the liquid phase that cannot leave the site. Therefore, hydraulic control is typically maintained as a combination of active pumping from the source zone, combined with extraction of water as steam by the vapor extraction system.
How is hydraulic control of a TTZ monitored and maintained?
Several direct parameters can be monitored throughout an ISTR project to assess the hydraulic control within a TTZ. These direct parameters include:
- Measuring the hydraulic head and pressure in extraction or monitoring wells (both inside and outside the TTZ) to confirm that inward hydraulic gradients are being maintained. Opening monitoring wells during operations can be a challenge, though, and pose some safety concerns.
- Monitoring subsurface temperatures both along the perimeter, as well as outside the TTZ, to ensure that warm fluid is not flowing out of the TTZ.
While these parameters are important to track during operations, perhaps the best metric for determining whether hydraulic and pneumatic control within an ISTR TTZ is being maintained is through the vapor and water balance. While no vapors are injected during a thermal project, the vapor balance is coupled directly to the vapor extraction flow rate from the extraction wells. All vapors extracted from the subsurface are either pulled in from areas outside of the TTZ or are a result of the pneumatic gradient being established, pulling vapors from the surface of the site into the treatment zone.
Maintaining a solid site water balance is a little more involved. The water balance kept during the operations of an ISTR project tracks the net injection and extraction of fluids, such that an overall net removal is maintained. The water balance is an important parameter for all thermal remedies, but it is especially important at sites that use electrical resistance heating (ERH) and steam enhanced extraction (SEE) technologies where a sizable quantity of water is injected as cooling and wetting fluid to electrodes (ERH) or as steam (SEE).
To maintain hydraulic control during ERH and SEE, the removal of water must be larger than the injection rate combined with the natural inflow of groundwater within the treatment volume. To maintain hydraulic control during ERH and SEE projects, we aim to maintain an extraction rate of water between 50% and 100% higher than the injection rates to have a good contingency in the water balance. For steam specifically, the water balance needs more contingency, since the steam bubble displaces the groundwater, and therefore adds to the liquid extraction volume required to not push any water outwards.
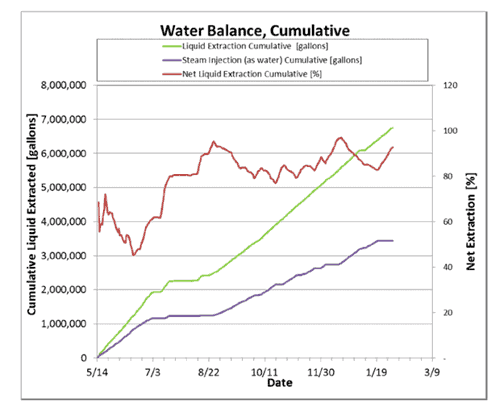
In the example water balance above, twice as much water was extracted than injected during a SEE project. The net liquid extraction remained within the 40-100% range throughout operations, indicating that the site maintained good hydraulic control throughout. Like always, we kept a close eye on the site energy balance as well, since too high of a net extraction will cool the thermal TTZ unnecessarily.
How is pneumatic control of a TTZ monitored and maintained?
Parameters for assessing whether a TTZ has achieved pneumatic control are fewer than hydraulic control but include:
- Frequent monitoring of the pressure at pressure monitoring points, both within the ISTR wellfield as well as along its perimeter
- Periodic measurements of the vacuum applied to the vapor extraction wells within the wellfield
In both of the assessment parameters mentioned above, these metrics are being tracked to confirm that the vapor flow across the wellfield remains balanced and that the overall extraction of the contaminant mass is efficient.
It is important to note, however, that while the goal for achieving pneumatic control is to have a balanced wellfield with nearly equal flow at all extraction points, some subsurface conditions may cause some wells to show positive pressure, or no pressure or vacuum at all. Part of the reason why thermal remedies are so successful in remediating even tight materials is the in situ steam generation in the small isolated pores of the tight clays and silts, that builds up local pressures, generate microfractures to the extraction points, and therefore serve as pathways out of the tight material. These local pressures do not immediately indicate pneumatic control has been lost, but that the thermal mechanisms are doing their job.
Finally, screening of ambient air within the wellfield using a photoionization detector can help in assessing whether pneumatic control has been achieved. If fugitive emissions are identified within the wellfield, this may indicate a failure in vapor extraction and an overall loss of pneumatic control or a flaw with the installed vapor cap.
One can imagine that if hydraulic and pneumatic control is not maintained during thermal remedy, the contaminants will be spread in the subsurface, causing the overall project objectives to not be met, or substantially increasing the timeline for meeting the objectives. Understanding how pneumatic and hydraulic control is maintained during operations and the metrics used to assess these parameters can help our experts optimize system performance to ultimately achieve project goals.
If you would like to learn more about other parameters and data considered during a thermal remedy, send me an email or watch our on-demand webinar, titled, “Data Management: The Most Underrated Aspect of Thermal Remediation Operations.”
02.24.22
Hillary Easter
Hillary is one of our Project Managers and is responsible for the effective execution of a complex project within scope, schedule, and budget. She is responsible for establishing the scope and schedule with the client at the outset of a project; managing the p...