Environmental consultants know that even the most carefully researched and meticulously planned project cannot anticipate every possible scenario. But when unexpected challenges arise, how is adaptive management utilized with in situ thermal remediation implementation?
Expect the unexpected; never say never. As I approach 10 years of working here at TerraTherm, these have become my mantras when approaching the operations phase of work at our thermal remediation projects.
Heating the subsurface is no small task. Once the thermal remediation is underway, there are significant reasons to keep the system operating until it is done. Some of these reasons include schedule, inefficiency and cost associated with turning the heating on, off, and then back on, and the need to continue to operate the extraction and treatment systems, even if the heaters are off. It is important to bring an attitude of dexterity and flexibility to accommodate and promptly react to normal operational issues as well as unanticipated challenges to keep thermal remediation projects on track, so they achieve the remedial goals on time and within budget.
The Importance of Timing
Due to the aggressive nature and significant daily operating cost of a thermal remedy, operational issues must be addressed immediately, typically within hours or days rather than weeks. Extended treatment system shutdowns can lead to fugitive emissions and each day of standby for a thermal system can cost thousands of dollars and may set back the total remediation progress. Additionally, remedies implemented in populated settings and sensitive environments often draw a high degree of public focus. If problems are encountered, rapid reactions and responses are needed to ensure the continued operation of the thermal system.
With the fast-paced and dynamic nature of thermal projects, coupled with potentially uncharacterized contaminants or subsurface features, project teams need to be ready to act quickly. That’s why implementation of a robust data collection program, as well as routine system inspections are essential to be able to quickly identify, troubleshoot, and address any unusual observations.
Some of the Most Common Challenges
Many operational challenges are related to the chemicals being treated. Thermal remedies are source zone treatments, and it is not uncommon that the contaminant mass loading on the treatment system is an order of magnitude more or less than what was estimated in the site conceptual model and design. Thermal remediation sites have been treated where the daily contaminant removal rate exceeded 25,000 lbs/day, so the selection of appropriate treatment system components is critical. Treatment in phases can be the solution to stagger the mass removal and decrease the peak loading on the treatment system.
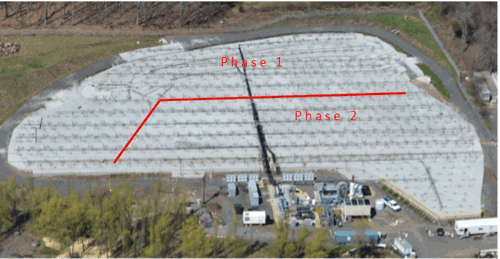
Another operational challenge that needs immediate focus is biofouling and emulsifications in the liquid treatment system. The heated environment, frequently accompanied by increased nutrients and available carbon, often serves as the perfect stage for biological growth that affects treatment system performance and can lead to permit exceedances. At the same time, changes in constituent properties with temperature and mechanical disturbance of the chemical mass may create emulsifications in tanks and transfer pipes. Thus, immediate attention is required, the type of problem must be identified and the addition of the right mix of controlling agents needs to be initiated. Jar tests conducted in the field can be a way to determine in real time and address the often site-specific type of biofouling and emulsification encountered.
Also, it is not unusual to have to respond to phenomena such as faster breakthrough than expected of site contaminants on the vapor or liquid carbon adsorptive vessels, fugitive odors or emissions, or areas where heat up and/or extraction is not as designed. The engineering team must work closely and promptly with vendors to expedite additional supplies to the site, evaluate and control treatment system issues, pre-emptively screen for fugitive emissions and odors or other signs of potential problems, and mobilize crews to investigate and address any heating or vapor/liquid extraction and treatment performance in areas that are not responding per our modeled expectations.
For instance, at a recent Manufactured Gas Plant (MGP) site cleanup, the temperature monitoring system quickly identified temperatures spiking several hundred degrees above the surrounding subsurface temperatures, indicating subsurface smoldering of coke, coal tar, and/or related materials. While smoldering was effectively destroying site contaminants in situ, safety was a concern. Rapid diagnosis and response resulted in mobilizing and installation of a network of water dousing points, to control and contain the smoldering inside the treatment zone and prevent uncontrolled spread of the reaction. At the same time, the extraction strategy was altered to limit the amount of oxygen delivered to the smoldering area.
Given the possibility of unexpected conditions or performance at thermal remediation sites, the field staff must be trained to respond 24/7 to quickly work with clients and project stakeholders to find and implement suitable remedies for the project to stay on track to cost-effectively meet the remedial goals within the desired schedule.
Contact me if you would like to learn more about potential issues at thermal remediation sites or a specific site you may have and how they can be identified and addressed promptly to minimize impacts to project performance.
10.21.21
Alyson Fortune
Alyson Fortune joined TerraTherm in 2012 as a Senior Scientist with over 15 years of experience in the environmental industry, including experience with source testing, analytical laboratory testing, and environmental consulting. Alyson is acting as the data q...